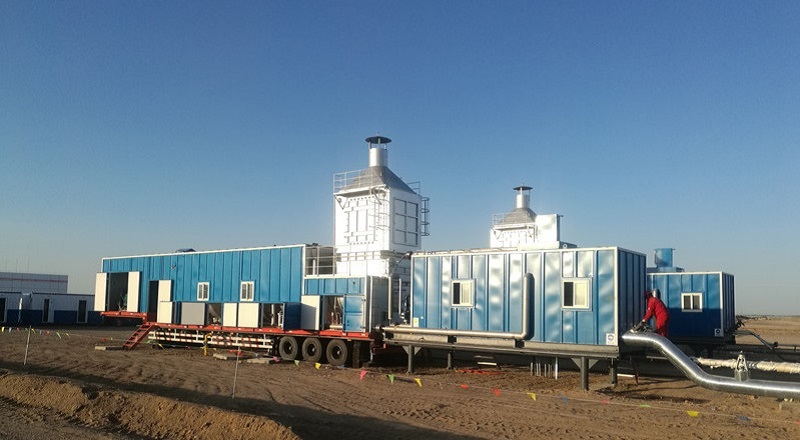
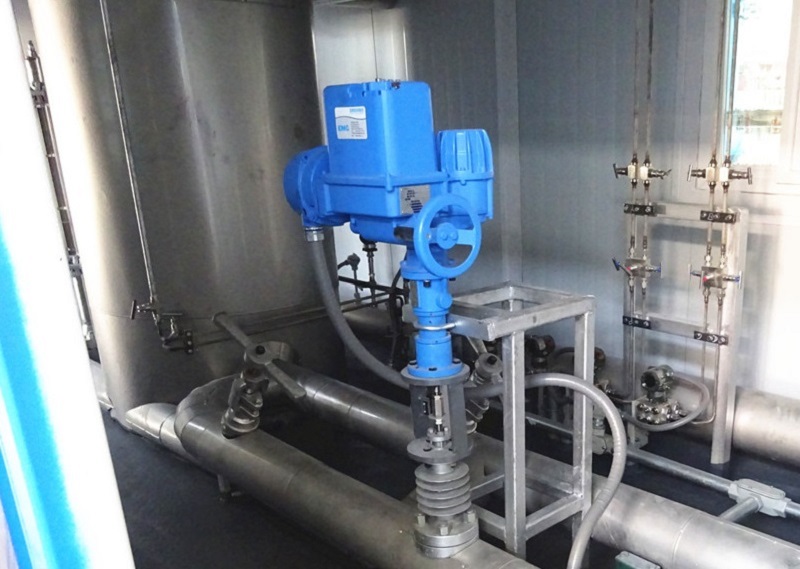
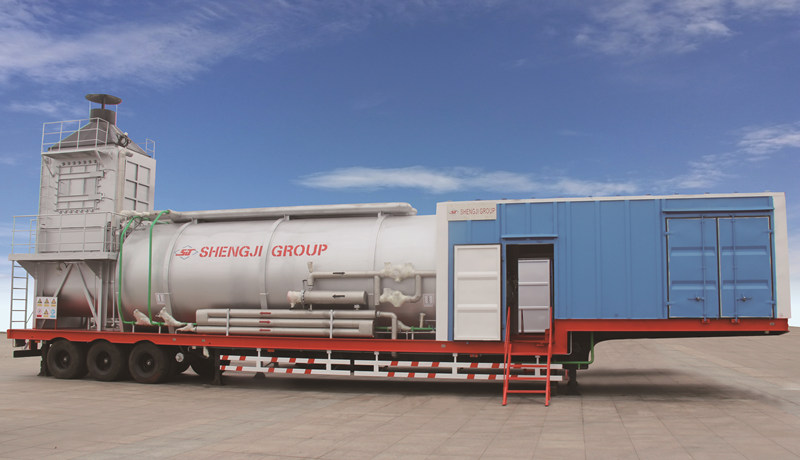
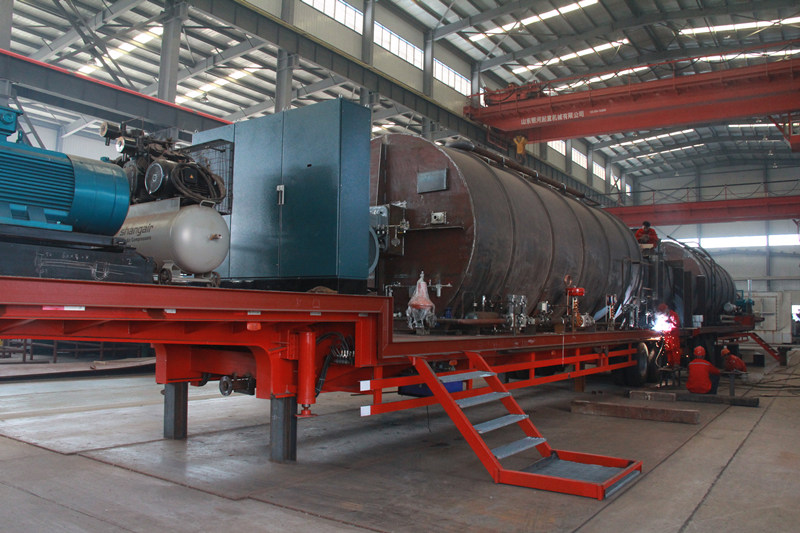
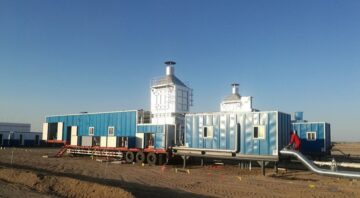
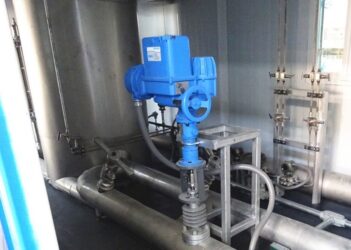
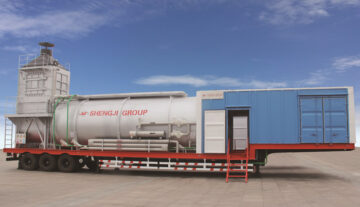
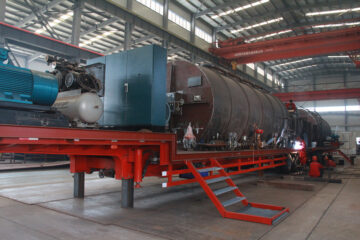
Oilfield steam injection boiler, also known as wet steam generator, is one kind of special steam injection equipment for heavy oil recovery in oil fields. It uses the heat generated by the combustion of gas or fuel oil to heat and vaporize water, generates high temperature and pressure wet steam to inject into the well, and heats the crude oil in the reservoir to reduce the viscosity of heavy oil, thus increasing the fluidity of heavy oil and greatly improving the recovery of heavy oil. ShengjiPetro can design and produce various types of oilfield steam injection boilers.
High-dryness Steam Injection Boiler
Superheated Oilfield Steam Boiler
Produced-water Oilfield Steam Generator
Desulfurization and Denitrification Oilfield Steam Boiler
Supercritical Oilfield Steam Injection Boiler
The Action of Superheated Steam
The viscosity of heavy oil is very sensitive to temperature. As long as the temperature rises by 8~9℃, the viscosity will decrease by one time. If high pressure superheated steam is injected into the reservoir for thermal recovery, not only the single well production can be greatly increased, but also the recovery can reach 50%~70%.The key to improve oil recovery is to improve the quality of steam injected into the reservoir. The higher the dryness of the steam, the greater the heat carried by the steam per unit weight, the higher the effective heat injected into the reservoir and the higher the production and recovery. According to relevant data, after superheated steam huff and puff technology is used in heavy oil recovery, the output can be increased by 3~8 times and the recovery can be improved significantly. Therefore, superheated steam injection is an effective way to increase the yield of heavy oil.
How the Superheated Oilfield Steam Boiler works
The radiation heat exchange section, convection heat exchange section and water-water heat exchanger in the front stage of superheated steam injection boiler are basically the same as the normal one in structure. 70-80% wet steam is produced in the front stage during heat exchange. Then, about 99% of the dry steam is separated by the high-efficiency steam-water separator(14) and fed to the superheated section for heating, which further increases the steam temperature to become superheated steam (460 ~500℃). The superheated steam is then mixed with the unsaturated brine separated from the steam-water separator. After mixing, the temperature drops to about 370 C and the steam dryness is more than 90%. Finally, high-dry steam is injected into the well.
Its main advantage is that the steam process from 80% to more than 90% occurs outside the boiler body. It effectively avoids the danger of tube burst due to uneven salt precipitation in heat exchanger tubes in furnace caused by high heat flow density of flame radiation/flue gas convection heat exchange
.
Superheated Oilfield Steam BoilerSpecial Component
1.Convection Section& Overheating Section
1). The convection section in the upper part realizes the heat transfer from low temperature water to high temperature water.
2). The lower high temperature convection section realizes the convection heat transfer process from saturated steam to superheated steam. Because the heat flux density here is lower than that in the radiation section, coupled with the scouring effect of high velocity of superheated steam, a small amount of saturated water will not cause internal salt precipitation and scaling.
3). The convective heat transfer area is increased, and the exhaust gas temperature is effectively reduced to meet the national energy conservation and environmental protection requirements.
4). The control technology of dryness and oxygen content in flue gas is applied to ensure the stable and balanced operation of thermal efficiency, so that the steam injection boiler is always in the state of high thermal efficiency, so as to achieve the purpose of energy saving and efficiency increasing.
The steam-water separator is a spherical or vertical vessel with built-in high-efficiency separator. A defoaming separator is set at the steam outlet to further separate small water droplets in the steam. The figure shows a newly produced 15t/h steam-water separator. Four-stage steam-water separator is used internally, which makes the separation efficiency up to 99% and meets the steam quality requirements of the superheater.
Steam-water mixer utilizes the differential pressure flow suction effect between superheated steam and separated unsaturated brine to spray separated brine into superheated steam in a foggy manner and mix it with superheated steam, thus reducing the temperature of superheated steam and keeping the final steam in an overheated state.
Oil and Gas Burners.
Model: KRBY1040
Brand: UNIGAS
Origin: Italy
Output power: 2550-13000kW
Atomization mode: air/steam atomization
The burner's fan is highly integrated with the combustion system, providing programmed ignition, purge, flame monitoring and flame-out protection to adjust fuel consumption as load changes.
4.High Pressure Plunger Pump
Use high pressure five cylinder plunger pump
Model: 5GP125-15/21
Brand: Ningbo Heli
Output power: 132 kW
Use media: purified produce-water
Operating temperature: 60-80℃
Output pressure: 21MPa
Model Number: DMC65 B1-16
Brand: DREHMO
Origin: Germany
Valve body nominal path: DN32
Valve body origin: Dalian Zhongyi
Superheated Oilfield Steam Boiler Parameter
Rated evaporation: 23t/h
Fuel: Crude oil/Natural gas
Rated working pressure: 17.2MPa
Boiler thermal efficiency: ≥91% (fuel oil)/≥92% (fuel gas)
Rated working temperature: 360℃
Operating steam superheat: ≥5℃
Operating exhaust temperature: 160℃ (fuel oil)/130℃ (fuel gas)
Control method: PLC + touch screen + industrial computer
Loading method: Skid/Vehicle
Superheated Oilfield Steam Boiler Features
Shengji Petroleum Pumping Unit Manufacturing Plant is one of the main branches of Shengji Group. It is a professional manufacturer specializing in the development, design, production, remanufacturing, maintenance, sales and service of pumping units. The factory has 235 employees, more than 130 sets of various large and medium-sized mechanical processing equipment, fixed assets of 12 million yuan, annual output of 1,200 pumping units, and annual sales income of 200 million yuan.
There are 4 senior engineers, 12 intermediate engineers, 7 assistant engineers, 4 senior technicians and 12 technicians in the pumping unit. Intermediate and senior workers account for more than 90% of all workers. The superb technical level of employees provides a technical guarantee for the production of high-quality pumping units.